Uma parcela significativa das organizações da atualidade já tem ciência dos benefícios advindos da implementação do Lean para gestão de processos, e aplicam suas ferramentas no dia a dia, objetivando com isso a eliminação dos desperdícios e a melhoria contínua.
Contudo, é comum que esses benefícios não sejam explorados na totalidade de seu potencial devido ao frequente surgimento de barreiras culturais, organizacionais ou estratégicas, que causam nos líderes incertezas e preocupações, e desmotivam os times operacionais à manutenção da cultura Lean na organização.
Entender quais são essas barreiras e como desconstruí-las ou contorná-las é fundamental para que as iniciativas de melhoria não fiquem sufocadas sob a pressão para atingir resultados diários, e para que as empresas sejam capazes de se manterem relevantes no cenário competitivo da atualidade.
Quer saber quais são os principais desafios encontrados pela Nortegubisian em projetos de implementação do pensamento Lean nos nossos parceiros? Continue lendo nosso artigo!
Casa desarrumada
Ambiente produtivo desorganizado, sujo ou inseguro
Os conceitos do 5S são a base para a implementação da cultura Lean, o que torna fundamental o entendimento do nível de maturidade da organização quanto à sua aplicação.
Líderes não devem apenas promover eventos 5s isolados, mas conduzir suas equipes a uma mudança cultural mais profunda, de forma que a manutenção do ambiente faça parte da responsabilidade individual de cada um.
Processos sem padronização
“Onde não há padrão, não pode haver melhoria.” (Taiichi Ohno)
“Não existe controle sem padronização.” (Juran)
É comum encontrar organizações que possuem documentos de registro de trabalho padronizado, elaborados de forma minuciosa por equipes de engenharia de processos, mas que não são vividos pelo operacional. Executar frequentemente o “Genchi Genbutsu” (vá e veja por si mesmo) é essencial para se ter visibilidade do nível de transparência atual dos processos.
Envolver adequadamente os times operacionais na construção do Trabalho Padrão ajuda a garantir que estes estejam alinhados e engajados em sua execução.
É importante ter em mente que todos os níveis organizacionais devem contar com certo grau de padronização.
Ausência de clareza e/ou coesão estratégica
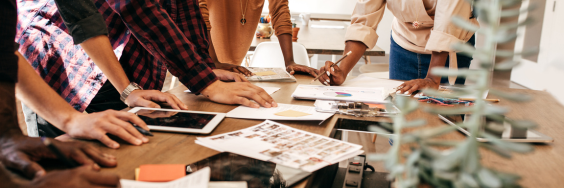
Indicadores conflitantes, de difícil compreensão ou medição e metas inatingíveis são exemplos de barreiras estratégicas para implementação da cultura Lean na indústria. Líderes vivem em dinâmica constante de “cabo de guerra”, desperdiçando esforços para executarem planos de melhoria desalinhados com objetivos da organização ou de outros departamentos.
A prática regular do Genchi Genbutsu por todos os níveis ajuda não apenas a padronizar e otimizar os processos, mas também a entender melhor as dores dos times operacionais, definir metas mais concretas e realizáveis e promover uma maior aderência aos objetivos estratégicos.
Muitas empresas que já possuem maturidade para desdobrar sua estratégia em metas que se conectam verticalmente, ainda sofrem com objetivos que se conflitam horizontalmente. Como reduzir custos sem perder produtividade? Como eliminar desperdícios de produtividade sem comprometer qualidade ou segurança?
É importante que existam canais de comunicação entre as áreas, e que estes sejam abertos e livres de ruído. Empregar metodologias como o S&OP também ajuda a manter alinhamento através dos departamentos.
Pouco engajamento da alta gestão
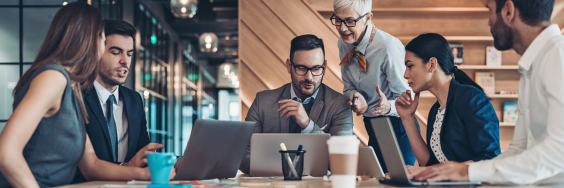
Embora grande parte das mudanças necessárias para a implementação da cultura Lean girem em torno do nível tático-operacional, muitas iniciativas fracassam por falta de envolvimento das lideranças do nível gerencial e estratégico.
Quando a atenção da alta gestão está exclusivamente em outros objetivos ou projetos, líderes encontram dificuldades em propagar as mudanças culturais necessárias através dos demais níveis da organização, dificultando a consolidação e difusão dos ganhos de curto prazo alcançados. Times operacionais se desmotivam diante da limitação de tempo e recursos para implementação das ações de melhoria e tendem a retornar à estaca zero.
Para colher os melhores frutos da excelência organizacional, não basta fazer Lean, é necessário pensar Lean.
Falta de foco na implementação do Lean
Mesmo cumprindo todos os requisitos para implementação do Lean, é possível não atingir os resultados esperados por não conseguir fazer as ações saírem do papel num ritmo adequado. Ainda que haja um plano de ação detalhado, com todas as oportunidades de melhoria mapeadas, os líderes podem se perder na execução e acompanhamento de diversas atividades simultâneas, ou acabam implementando mudanças que agregam mínimo valor e exigem grandes esforços.
É importante priorizar as atividades adequadamente de acordo com sua relevância geral para a organização. Utilizar ferramentas como a matriz BASICO e o princípio de Pareto para identificar quais são as poucas ações críticas, que agregam maior valor com menor esforço, permite que organizações comecem a alcançar os primeiros resultados muito mais rapidamente. Priorizar duas ou três tarefas por vez torna possível manter um fluxo de entregas mais consistente.
Então, se você também enfrenta esses desafios na sua empresa e precisa de ajuda para implementar as ferramentas Lean na sua organização, entre em contato conosco. Também continue nos acompanhando no blog, LinkedIn, Facebook e Instagram para mais conteúdos como este!
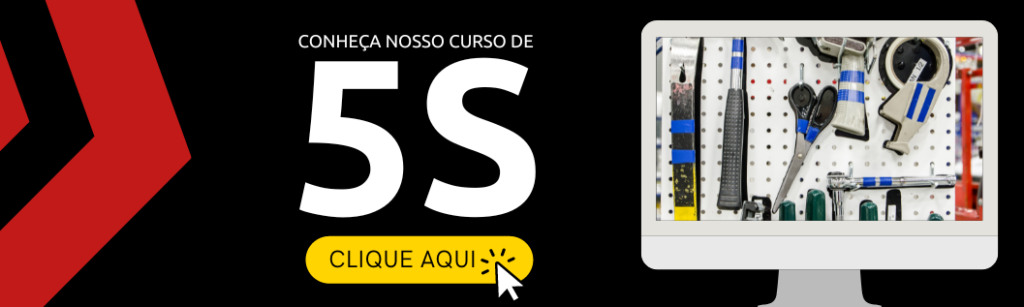