Desafio
Atuando desde 1936, esta importante empresa do setor de produtos químicos para a construção civil no Brasil, buscou a Nortegubisian para um desafio: realizar um projeto de layout do novo Centro de Distribuição (CD) que atendesse às necessidades atuais de armazenagem na companhia e possibilitasse a otimização de toda a operação.
O atual centro de distribuição em São Paulo é abastecido por duas fábricas instaladas no Estado, uma no Nordeste e fornece materiais para diversas obras em todo o país. Com o crescimento dos negócios, começou a sentir dificuldades no escoamento de materiais e limitação de espaço para expansão do armazém.
Para solucionar esse problema, iniciou-se o trabalho de mudança do parque industrial para o interior do Estado, começando pelo novo CD.
Com o desafio aceito, a Nortegubisian aplicou os conceitos de Lean para entregar o layout do novo Centro de Distribuição visando a otimização de toda a operação e redução de desperdícios.
Confira abaixo como esse trabalho foi desenvolvido!
Desenvolvimento do Projeto de Layout
O desenvolvimento do projeto foi dividido em três etapas: Levantamento de Dados, Prototipagem e Dimensionamento.
Na etapa de Levantamento de Dados foram coletadas as informações de operação do CD atual, todo o histórico de recebimento e expedição dos produtos e as projeções de crescimento da empresa.
Para a coleta de dados da operação, a Nortegubisian acompanhou as operações do CD in loco e entrevistou os colaboradores dos setores. A partir das informações reunidas foi possível realizar o Estudo de Tempos e Métodos (ETM), que possibilitou a visualização de cada processo da operação – armazenamento, reposição, separação, conferência e carregamento – para determinação do tempo padrão de cada atividade como primeiro passo para a otimização do CD.
Após acompanhamento da operação in loco e estruturação do ETM, foram levantados os dados acerca dos CDs atual e futuro: layouts atualizados, ampliações futuras, tipos de estruturas de armazenagem, tipos de equipamentos de movimentação, relação de mão de obra por atividade.
Com esses dados e informações quantitativas do histórico de consumo de cada item no estoque, histórico da quantidade e frequência de recebimento e expedição e a projeção de crescimento foi possível definir o número de posições para cada grupo de produtos.
Os grupos de produtos se diferenciam pelo tamanho do palete utilizado, necessidade de área segregada (produtos perigosos e fontes de sujidade) e necessidade de paletização dos produtos separados para expedição.
Com as posições necessárias para armazenagem definidas, determinou-se os números de docas (tanto para recebimento, quanto para expedição), áreas de operação e corredores de movimentação e fluxo de pessoas.
Para dimensionarmos o número de docas, por exemplo, foi preciso entendermos a relação do fluxo de entrada e saída de materiais versus o tempo de execução característico de cada uma dessas operações, utilizando-se de conceitos Trabalho Padrão do Lean, mas também Cartas de Controle, do Seis Sigma. Tudo isso em sintonia com a capacidade de armazenagem, ou seja, procurando o trade off entre armazenar o máximo possível e fazer fluir os materiais, equipamentos e pessoas pelos corredores e docas de acordo com o Takt Time.
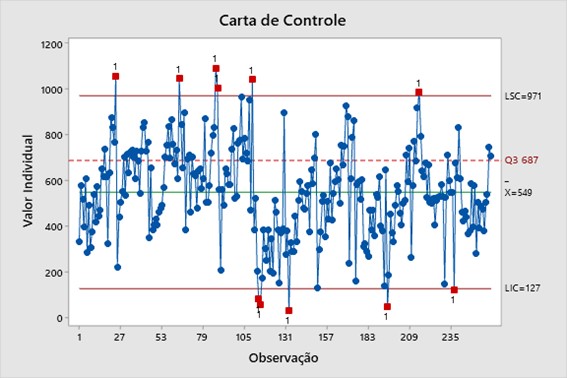
A mesma relação foi utilizada para o dimensionamento dos equipamentos de movimentação, em que foram escolhidas empilhadeiras elétricas para as atividades de armazenamento e reposição, já para as atividades de separação e conferência foram selecionadas paleteiras elétricas. A movimentação interna dos produtos entre as unidades produtivas e o CD foi selecionado rebocadores industriais com vagões. A escolha por equipamentos elétricos se deu por questões ambientais, com o objetivo de reduzir a emissão dos gases provenientes da combustão.
Com as informações obtidas até o momento, foi possível iniciar a prototipagem do CD com o número de posições necessárias, fluxo de movimentação de materiais e pessoas e adequação dessas estruturas as dimensões do terreno.
Devido a grande quantidade de SKUs e necessidade da operação de picking (separação) de produtos, foi verificado que a utilização de estruturas do tipo drive-in (ou drive-thru) não era possível devido as suas incompatibilidades com o processo. Assim, foram selecionadas estruturas de porta paletes com profundidades simples e duplas, respeitado a alocação dos produtos com base no giro e posições de picking. Essa decisão impacta diretamente nos equipamentos utilizados para armazenagem e reposição. As empilhadeiras foram selecionadas entre pantográficas e retráteis.
Em paralelo a definição da estrutura, realizou-se o estudo sobre os produtos considerando dois fatores: receita e giro, utilizando as curvas ABC e PQR combinadas.
Com a finalização das etapas anteriores, realizou-se a revisão do projeto junto a empresa e modelagem do Centro de Distribuição em 3D para melhor visualização. O estudo do layout em 3D permite a avaliação com maior precisão do ambiente, ajustes necessários e a facilidade de testar/avaliar novas ideias.
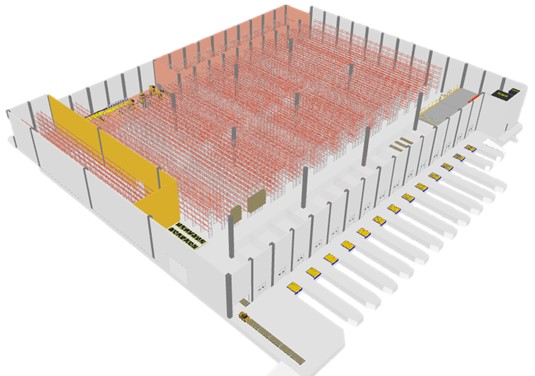
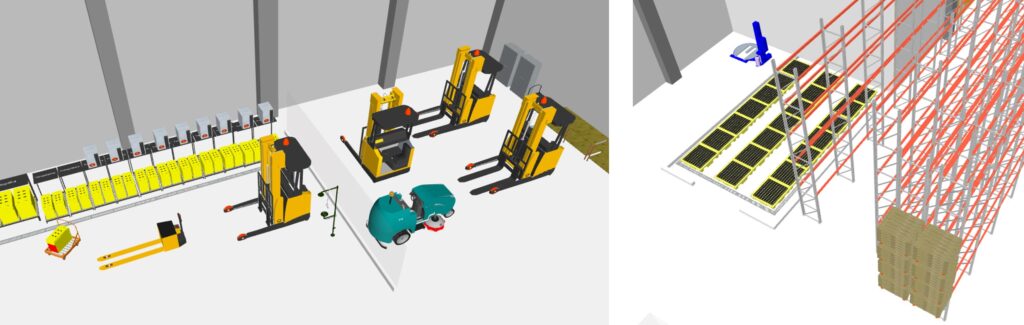
Com a aprovação do cenário apresentado, construiu-se a modelagem 2D do layout otimizado do Centro de Distribuição contendo todas as estruturas, marcações, cotas que será utilizado pela equipe de Engenharia e Arquitetura para a construção do CD.
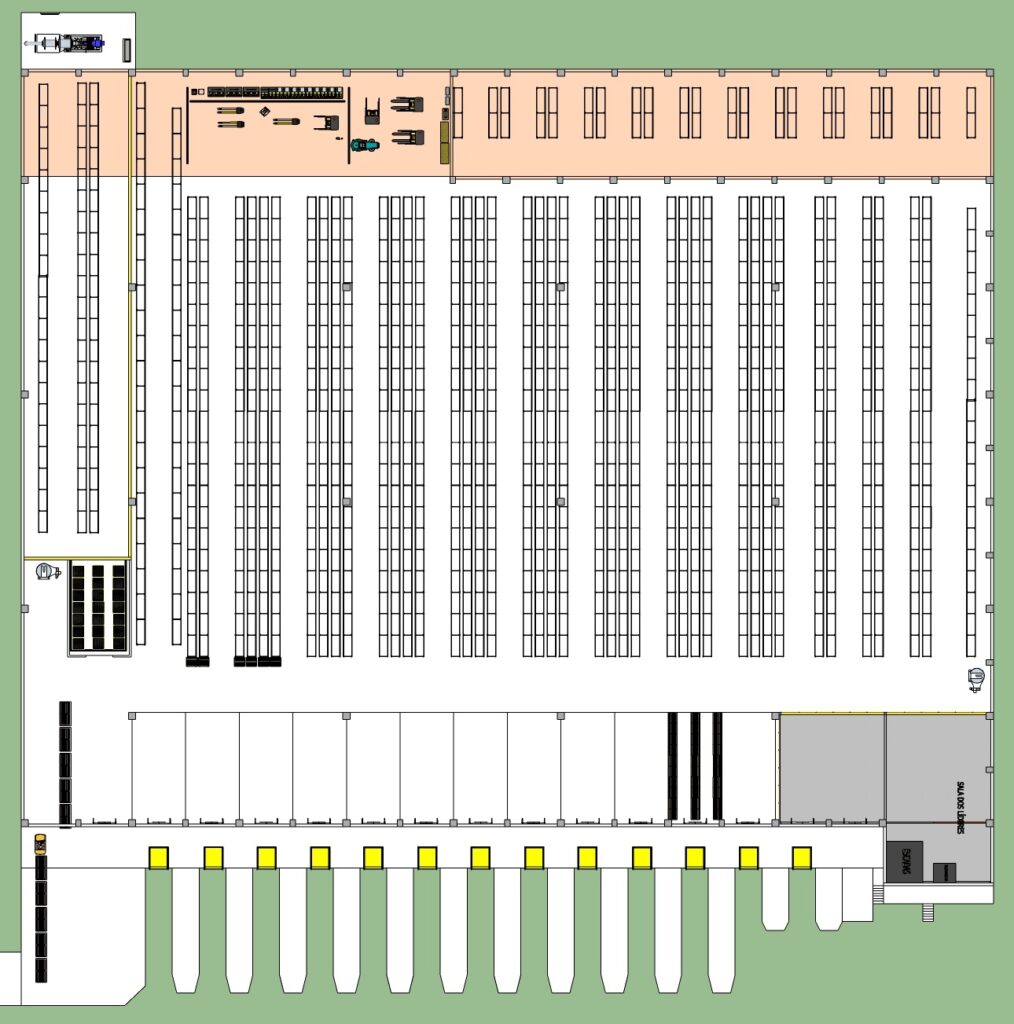
Com a conclusão do projeto do layout do Centro de Distribuição, realizou-se ainda o dimensionamento do número de recursos humanos necessários para sua operacionalização. Para isso, utilizou-se novamente os conceitos de Trabalho Padrão do Lean, aplicando os dados aos Gráficos de Balanceamento de Operadores (GBO), com o objetivo de se obter o número ideal de colaboradores, sem que haja ociosidade, mas ao mesmo tempo com capacidade para atender o Takt Time.
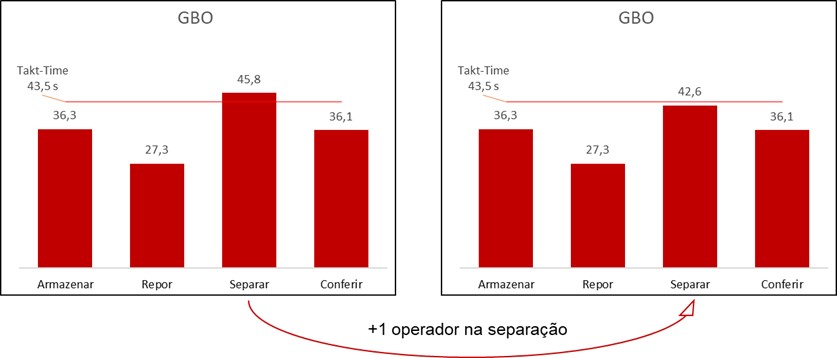
E por fim, montou-se a lógica de posição nas estantes, picking e abastecimento de acordo com as classificações ABC+PQR, itens com maior retorno financeiro e maior giro devem ficar mais próximos as docas de expedição visando redução de desperdícios, principalmente o transporte de materiais em excesso e a movimentação desnecessária de pessoas. Com relação a reposição, utilizou-se o sistema Kanban respeitando as particularidades dos itens e dos processos.
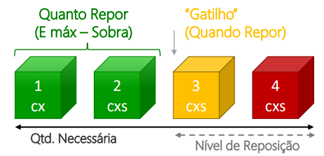
Resultados
Toda a concepção do layout do novo CD foi pensada para eliminar/reduzir os desperdícios do Lean em sua operação: esperas relacionadas aos carregamentos, excesso de movimentação de pessoas, transportes desnecessários dos materiais separados, conferências desnecessárias, etc. com o objetivo de obter a mais alta qualidade do serviço e menores custos de toda a operação.
O projeto da Nortegubisian do Layout otimizado do Centro de Distribuição resultou na entrega dos dimensionamentos de equipamentos de movimentação, recursos humanos e área de picking. Além do layout referente a fase 1 do projeto, com capacidade de armazenagem para até 2025 e áreas de operação já contemplando as fases 1 e 2 do projeto para até 2030.
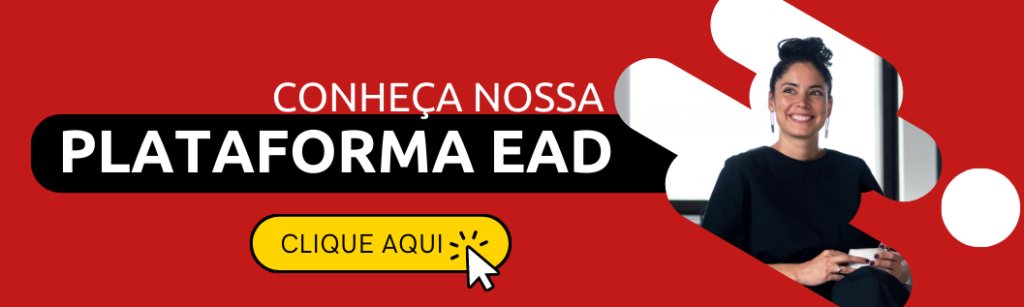
Também continue nos acompanhe no blog, LinkedIn, Facebook e Instagram para mais conteúdos como este.