Contextualização
Multinacional americana com mais de 60 anos de história e presente no Brasil há mais de 40 anos, a empresa concentra seus esforços em desenvolver e fabricar produtos com matérias-primas inovadoras.
É reconhecida mundialmente por suas linhas de produtos de higiene e limpeza com máxima qualidade e alta performance, entre elas, higiene hospitalar, limpeza industrial, indústrias alimentícias, cozinhas industriais, lavanderia, cuidados com as mãos, etc.
Limitada pelo espaço de sua planta produtiva, a intenção inicial era construir uma nova fábrica para ganhar capacidade e poder atender o crescente mercado consumidor. A matriz americana, entretanto, propôs o desafio de melhorar os processos na fábrica atual com objetivo de melhorar a performance e ganhar longevidade antes de um investimento em um novo espaço fabril.
Por este motivo, após intensa concorrência no mercado, a empresa escolheu a Nortegubisian como parceira nesta jornada. A escolha da Nortegubisian deu-se principalmente pela habilidade em planejar estrategicamente e pela facilidade em transformar os resultados por meio de uma abordagem hands on (mão na massa).
Etapas do Projeto
- Mapeamento inicial, elaboração do Mapa do Fluxo de Valor (VSM), identificação e priorização das oportunidades de melhoria
- Implantação do 5S, chamado carinhosamente de Programa SOL pela empresa, fazendo referência ao acrônimo Segurança, Ordenação e Limpeza.
- Implantação do modelo de gestão de estoques de matérias-primas e materiais de embalagens
- Projeto de reestruturação do armazém de produtos acabados e da expedição
- Implantação de planos de ação para aumento da capacidade produtiva
- Reestruturação do processo de planejamento, programação e controle da produção
Desenvolvimento do Projeto e Resultados
1. Mapeamento do Fluxo de Valor (VSM)
O mapeamento inicial foi realizado para cumprir os seguintes objetivos:
- Visualizar o processo completo, não só operações individuais
- Mostrar a relação entre o fluxo de informações e materiais
- Identificar desperdícios e suas fontes no fluxo de valor
- Fornecer linguagem comum para tratar dos processos
- Tornar visíveis as decisões sobre o fluxo e facilitar sua discussão
Como consequência, descobrimos que cerca de 95% das atividades no processo eram relacionadas a inspeções, movimentações, esperas e estoques, ou seja,atividades não agregadoras de valor.
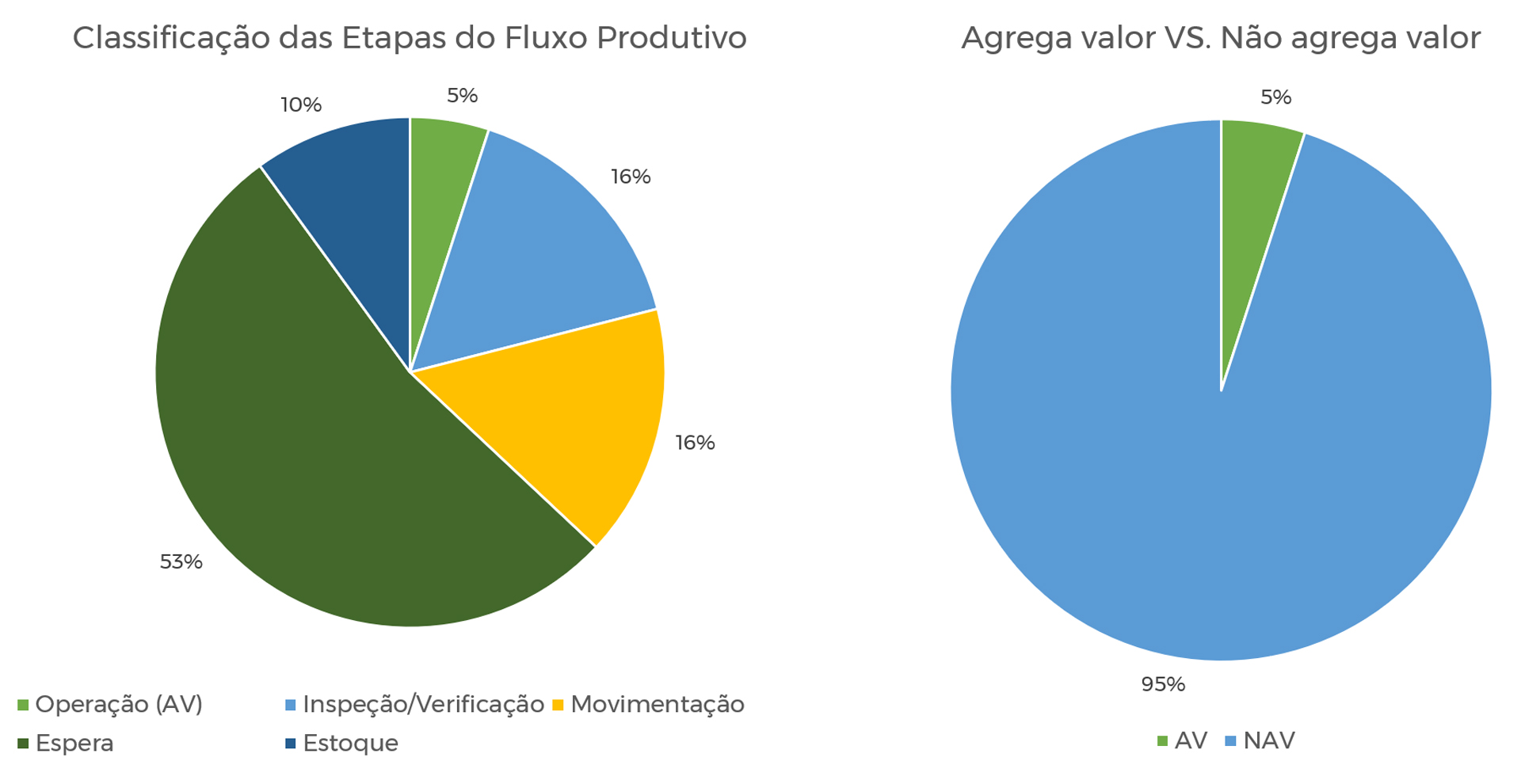
Com o Mapeamento do Fluxo de Valor (VSM) foram identificadas 82 oportunidades de melhoria. As principais oportunidades evidenciadas tinham relação com:
- Falta de organização, planejamento e padronização
- Falta de atendimento de pedidos (backlog)
- Stock outs de matérias primas
- Layout inadequado de produção, armazém de produtos acabados e de materiais para revenda.
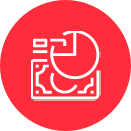
Diante de tantas oportunidades de melhoria, a saída foi prioriza-las. Para isso, utilizamos a Matriz BASICO.
B | A | S | I | C | O | |
Índice | Benefícios para a organização | Abrangência da solução | Satisfação dos funcionários | Investimento necessário | Impacto sobre os clientes | Capacidade de operacionalização |
5 | Vital importância | 71 a 100% | Muito grande | Baixíssimo (< 2k) | Muito grande | Muito fácil |
4 | Significativo | 41 a 70% | Grande | Baixo (entre 2 e 10k) | Grande | Fácil |
3 | Razoável | 21 a 40% | Média | Médio (entre 10 e 130k) | Médio | Médio |
2 | Poucos | 6 a 20% | Pequena | Alto (entre 130 e 200k) | Pouco | Difícil |
1 | Algum | < 6% | Indiferente | Altísssimo (> 200k) | Nenhum | Muito difícil |
Foram definidos 4 blocos de iniciativas, de modo a atacar as oportunidades prioritárias. Por questão de estratégia da organização foram focadas ações de baixo investimento e alto impacto. As iniciativas foram:
- Implantação do 5S (SOL)
- Implantação do modelo de gestão de estoques de matérias-primas e materiais de embalagens
- Projeto de reestruturação do armazém de produtos acabados e da expedição
- Implantação de planos de ação para aumento da capacidade produtiva
- Reestruturação do processo de planejamento programação e controle da produção
2. Implantação do 5S (SOL)
O Programa SOL, inspirado nos 5 Sensos da Qualidade, buscou a disciplina através da consciência e responsabilidade de todos os colaboradores de uma empresa, ou seja, visa aperfeiçoar o comportamento das pessoas através da mudança de hábitos e atitudes de forma a tornar o ambiente de trabalho agradável, seguro e produtivo.
Os principais objetivos do Programa foram:
- Maior produtividade dos recursos
- Melhor clima organizacional
- Melhoria da competitividade de organização
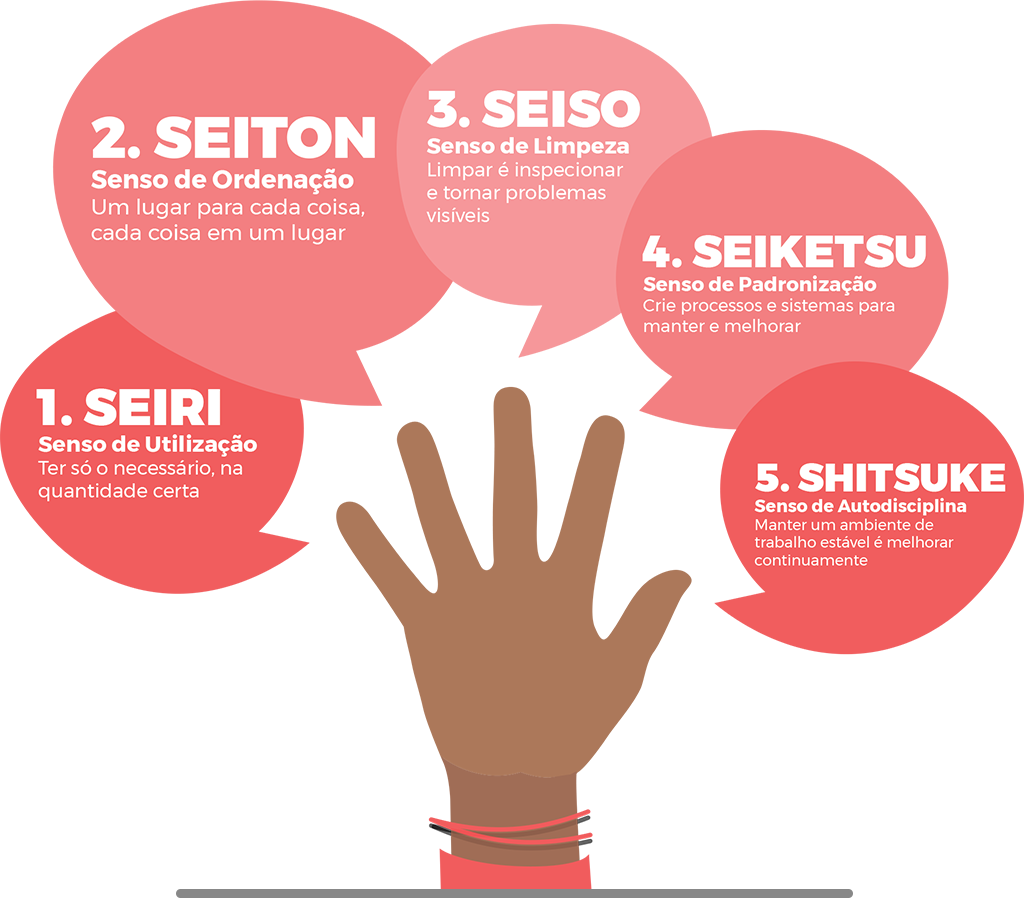
Foram criadas equipes por área da fábrica. Essas equipes continham um líder e um avaliador. As equipes tinham a missão de manter os padrões criados e melhora-los continuamente. Os líderes auxiliavam no estabelecimento e revisão dos padrões de Utilização, Ordenação e Limpeza, garantindo as condições necessárias para a manutenção dos resultados.
Todas as equipes utilizam quadros de Gestão à Vista para reuniões diárias com duração de 5 minutos para entenderem a evolução das tarefas em andamento e definição de novas ações, divulgação das ações e troca de experiências.
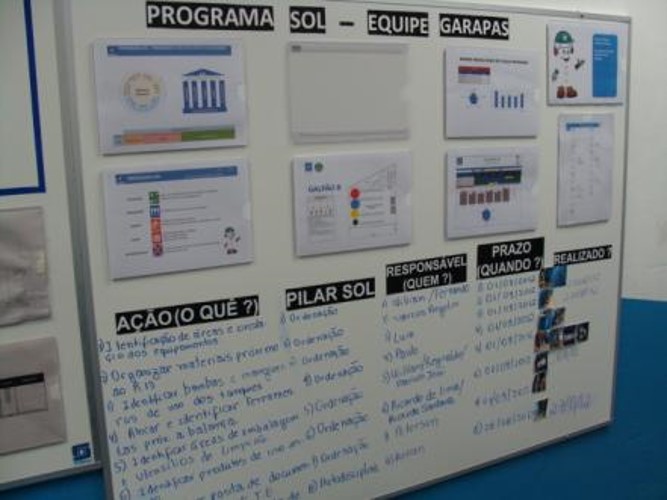
Os resultados foram incríveis. Veja a diferença dos padrões de Ordenação e Limpeza da área de Pesagem antes e depois da implantação do Programa SOL.
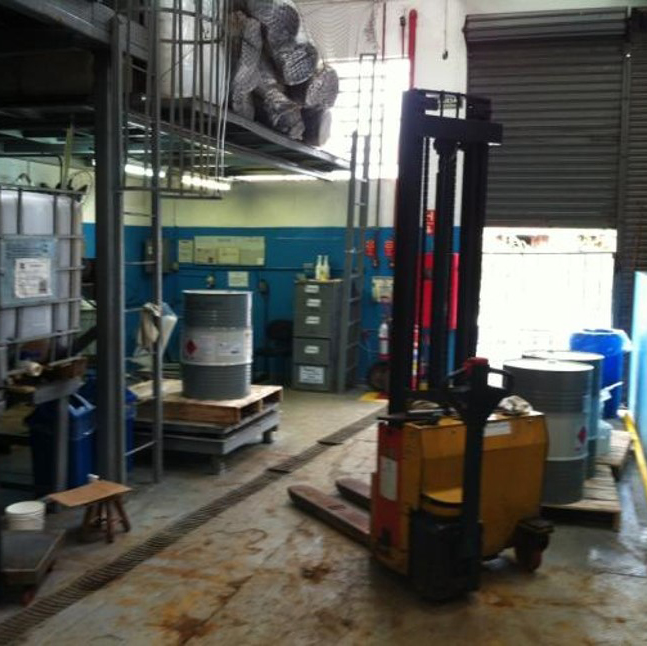
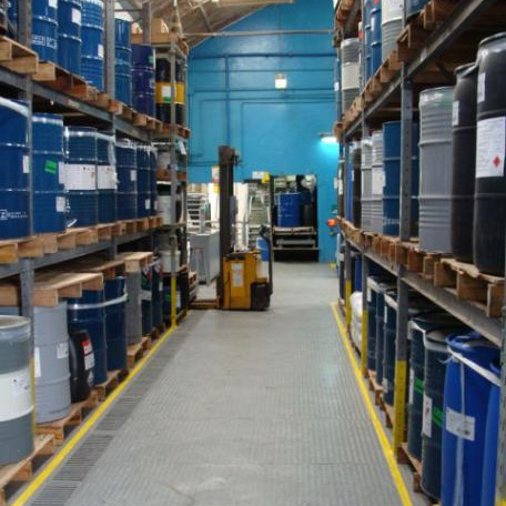
3. Implantação do modelo de gestão de estoques de matérias-primas e materiais de embalagens
Os principais objetivos relacionados a essa frente de trabalho foram:
- Reduzir os stock outs de matérias-primas e suas consequências na programação de produção
- Reduzir valor médio em estoque de matérias-primas
- Aproveitar melhor o espaço do armazém de matérias-primas
- Patronizar decisões de compra por meio de um modelo estruturado baseado na demanda.
O primeiro passo dado pela equipe de melhoria foi fazer a classificação ABC dos itens. Em seguida implantamos o Modelo Revisão Contínua dos estoques com a parametrização de estoques de segurança, pontos de pedido, revisão de lead times de entrega, lote econômico de compra etc.
Além disso, para auxiliar a área de compras, foi criada uma planilha de Tomada de Decisão. Nessa planilha, o comprador era capaz de fazer simulações de diferentes cenários como objetivo de dispor o máximo de informações pertinentes para auxílio na tomada de decisão. Esses cenários levavam em consideração os custos de gestão de estocagem e de compras. Dessa maneira, passou a ser possível negociar o preço e as condições de pagamento, custo do frete (FOB/CIF), lotes mínimos e múltiplos de compra e facilitar as compras casadas.
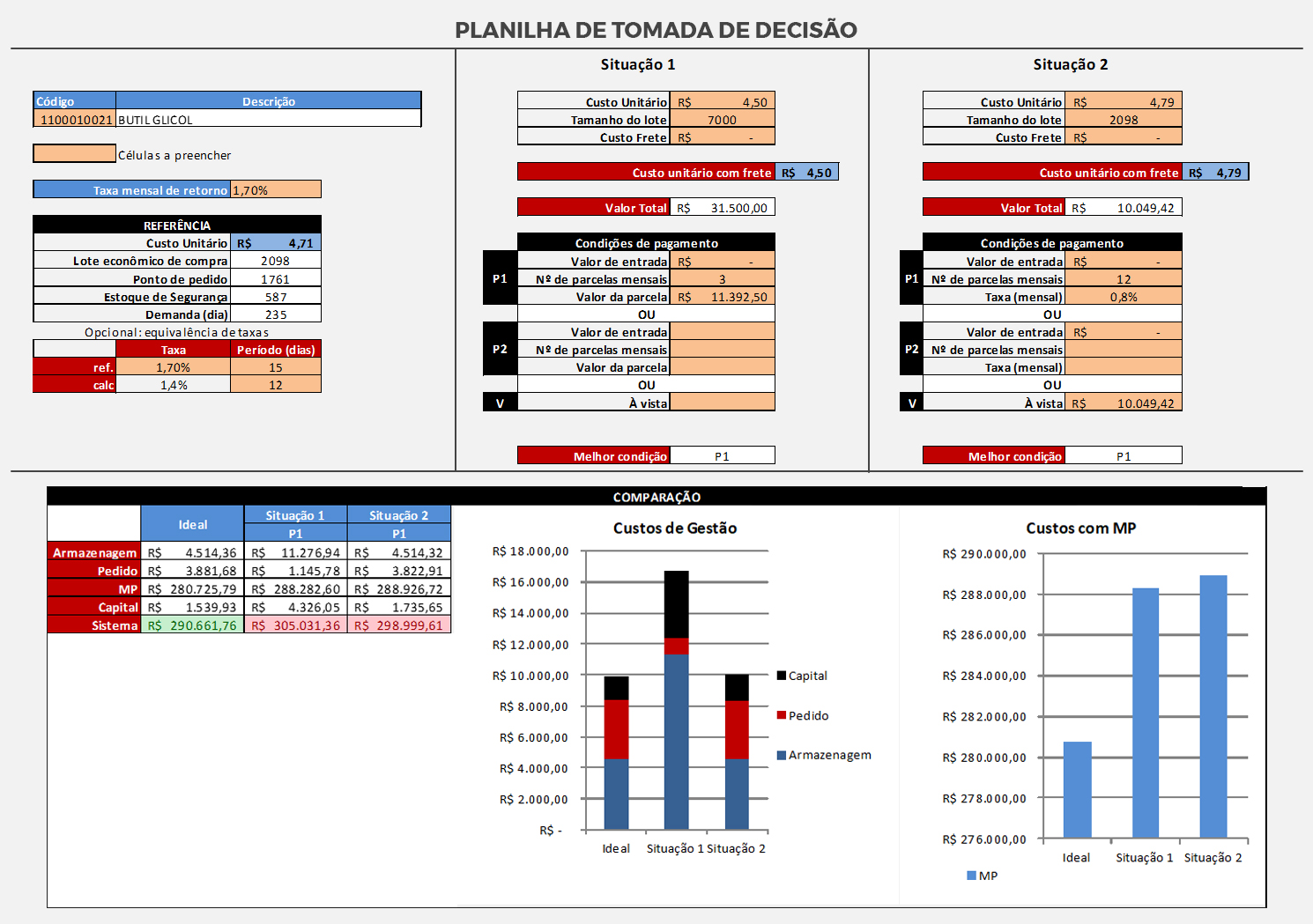
Com essa iniciativa houve redução de 20% do estoque, além de:
- Redução de alterações na programação da produção devido à falta de MP
- Criação de indicador de stock out
- Redução da ocupação de espaço no armazém de MP -> facilidade de fluxo e organização
- Compras efetuadas com modelo estruturado baseado na demanda.
Com relação as embalagens, foi observado que seu controle não era feito no sistema de informação da empresa. Por este motivo, a sua gestão não era adequada o que acarretava comumente a falta de embalagens na fábrica, devido à dificuldade de controle de estoque.
Para sanar esse problema, foi criado um modelo de Gestão Visual, controle direto no chão de fábrica através da sistemática do Kanban. Para cada embalagem foi criada uma região verde, amarela e vermelha similar a um supermercado. Toda vez que as embalagens consumidas atingissem a região amarela, o operador passou a providenciar a reposição do item. As áreas foram demarcadas no chão e nas estruturas de armazenagem.
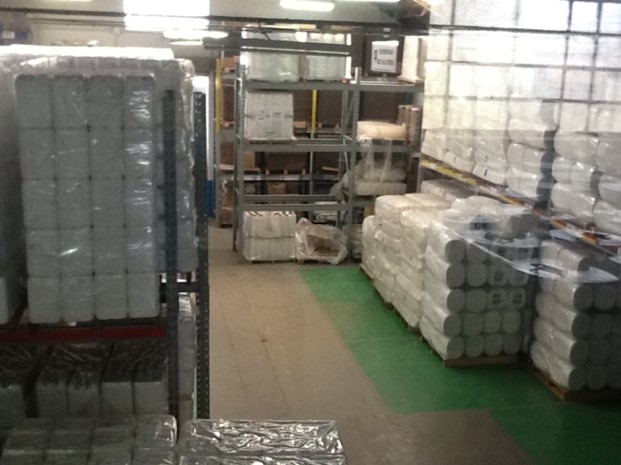
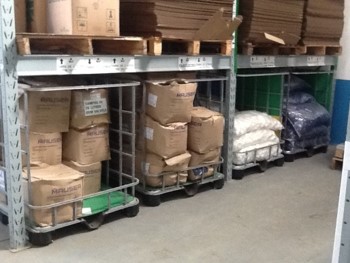
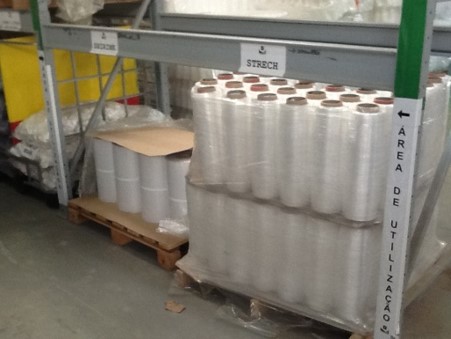
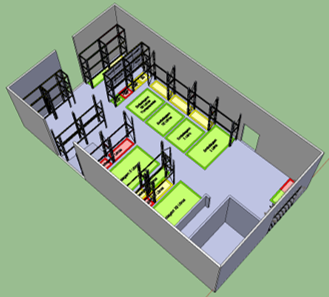
Para o entendimento e utilização correta da sistemática criada, foram elaboradas Instruções de Trabalho e todos os operadores foram devidamente capacitados.
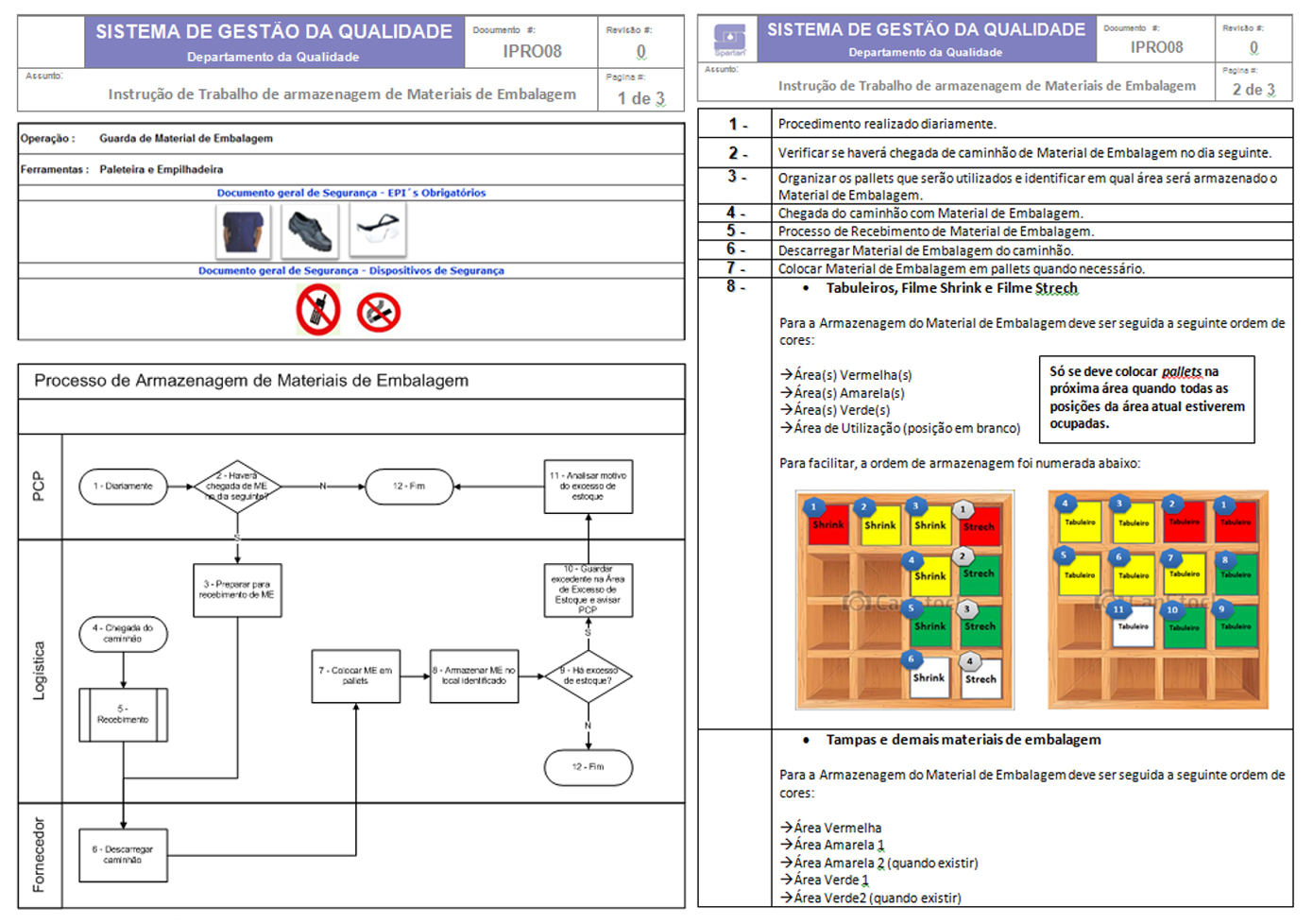
4. Projeto de reestruturação do armazém de produtos acabados e da expedição
No dia a dia, a empresa enfrentava muita dificuldade para fazer o picking do material devido ao layout indevido e encontrar os itens certos pela falta de endereçamento. Para isso, o processo era totalmente dependente da memória de cada um dos colaboradores da área para acessar os materiais necessários no momento picking, embarque e expedição dos caminhões.
Por estes motivos, o objetivo de trabalho foi:
- Melhorar o fluxo logístico interno de produtos acabados, acessando os produtos de forma rápida, produtiva e segura
- Maximizar a capacidade de armazenagem da área
- Liberar área em outros locais, de modo a melhorar seu fluxo logístico e/ou produtividade
- Reduzir perdas ou danos em produtos acabados e revenda.
Foram montadas estruturas porta pallet com rack móvel para o aproveitamento de espaço através da verticalização e seletividade. Empilhadeiras patoladas foram selecionadas para realizar a movimentação dos materiais devido a diminuição da largura dos corredores para otimização do espaço. Um estudo de fluxo de materiais,corredores e acesso foi realizado, visando a diminuição de movimentação. Áreas de picking antecipado foram criadas juntamente com a sistemática de janelas de expedição, o que resultou em diminuição drástica do tempo de liberação dos caminhões. Por fim o endereçamento dos materiais aumentando a produtividade de picking e facilitando o FIFO.
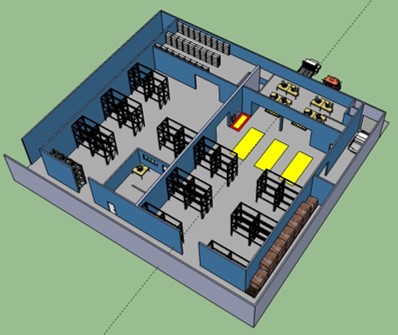
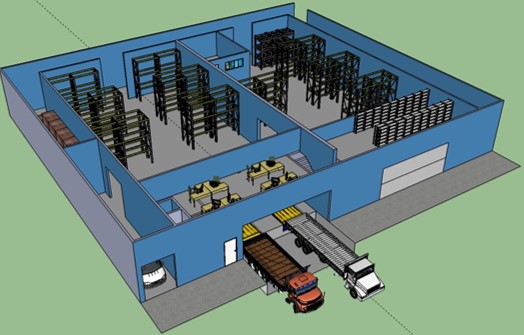
5. Implantação de planos de ação para aumento da capacidade produtiva
Durante a elaboração do VSM de Estado Atual, verificamos que a etapa de envase era gargalo. Por isso, todos os esforços foram direcionados para essa área, com o objetivo de aumentar a capacidade produtiva. Colocamos em prática o Estudo de Tempos e Métodos e realizamos as seguintes atividades:
- Decomposição das atividades em elementos de trabalho
- Coleta de tempos de cada elemento
- Balanceamento de trabalho por funcionário (Gráfico de Balanceamento do Operador – GBO)
- Cálculo de tempos de ciclo efetivos
- Distribuição do trabalho
Com a criação de um novo processo de envase foram alcançados incríveis 77% de aumento de produtividade da mão de obra. Foram estruturadas mais equipes com o mesmo número de pessoas e com maior disponibilidade, possibilitando maior taxa de produção.
Outro ponto importante foi a reestruturação do layout produtivo que proporcionou aumento de capacidade produtiva e redução de hora extra, melhor fluxo produtivo(movimentação), melhoria do ambiente de trabalho, maior capacidade de envase,maior produtividade dos recursos, com consequente redução dos custos de fabricação e melhor aderência às normas regulamentadoras.
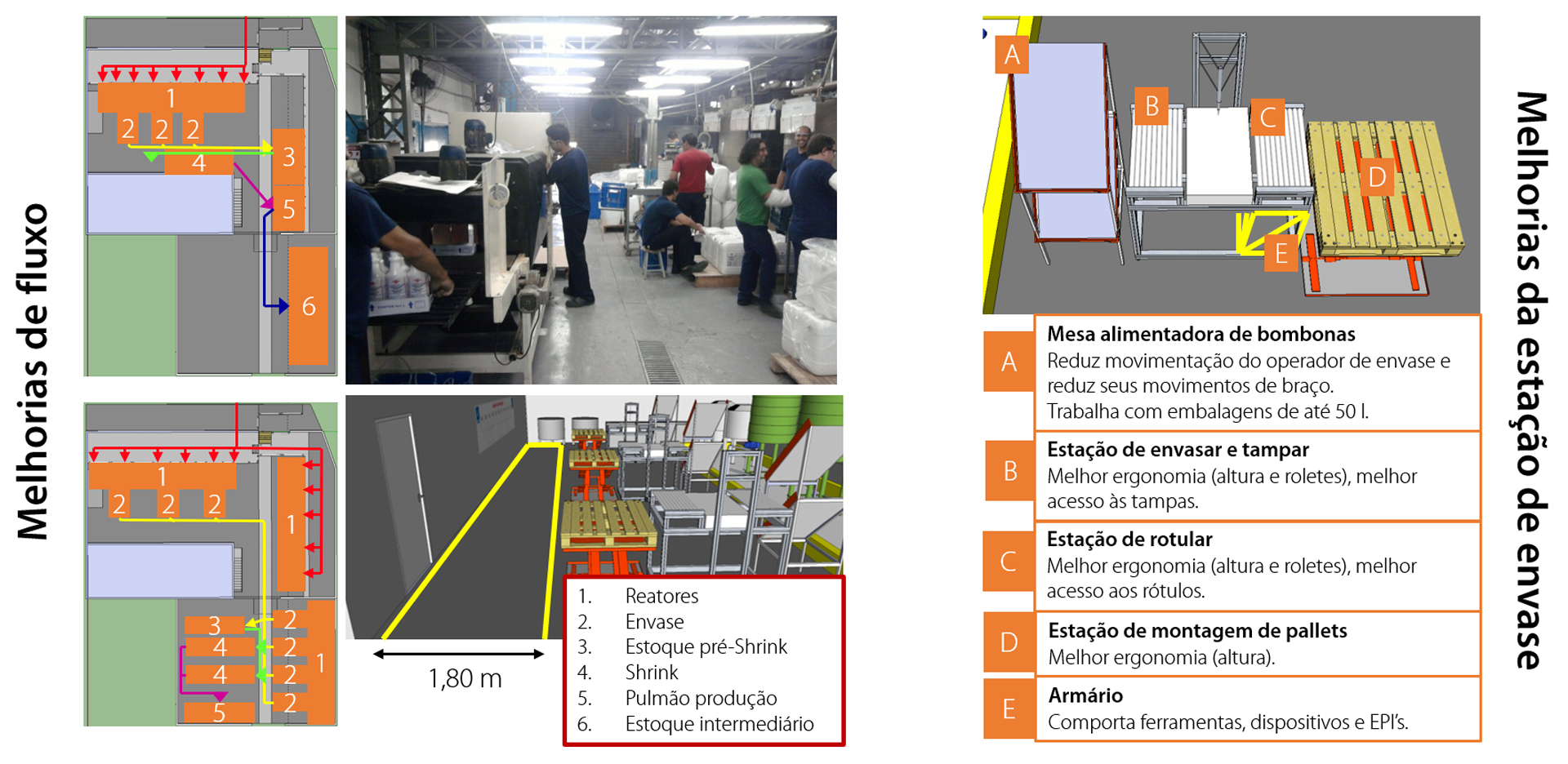
O tempo de pesagem também foi reduzido. Através da análise de consumo das Matérias Primas, foi decidido que aquelas que eram utilizadas com maior frequência seriam dispostas de forma a minimizar a movimentação do operador. Para as demais, foi introduzida a pesagem usando bombas pneumáticas. Através dessa iniciativa houve um aumento de 38,70% de capacidade, como pode ser observado na imagem abaixo.
Nesta fase do projeto, fomos surpreendidos por uma situação bastante interessante. A gerente financeira nos procurou para entender a razão dela ter percebido uma redução de 27% nos Gastos Gerais de Fabricação (GGF).
Essa situação nos deu a certeza de que estávamos no caminho certo.
6. Reestruturação do processo de planejamento, programação e controle da produção
Vários fatores motivaram a reestruturação do processo de planejamento, programação e controle da produção:
- Falta de produto acabado (backorder)
- Excesso de estoque de produtos e perdas decorrentes da perecibilidade
- Problemas de suprimento(embalagens e rótulos, por exemplo)
- Alto tempo para planejamento da produção
- Alta incidência de alterações na programação
- Alto tempo gasto preenchendo documentos/formulários
- Medidas de produtividade e disponibilidade insuficientes para estruturação de iniciativas de melhoria
Com relação à demanda e ao mercado, os seguintes desafios eram enfrentados:
- Ausência de uma avaliação sistemática dos lead times de entrega ideais por produto, família de produto,cliente ou tipo de cliente
- Ausência de avaliação sistemática de benchmarking de lead times de entrega praticados pelos principais concorrentes
- Demanda com alto componente sazonal intra-mês, nos fechamentos quinzenais e mensais
- Portfólio de 293 produtos(fabricação interna) com diferentes comportamentos em relação à volume e variação.
- Ausência de segmentação alguma na estratégia de produção – todos itens eram MTO.
A iniciativa para reverter esse cenário foi a estruturação do processo de Planejamento de Vendas e Operações adaptado para a realidade da empresa que passou a ser fundamental para o Planejamento, Programação e Controle da Produção.
Pouco a pouco as áreas de Vendas, PCP, Compras e Financeira passaram a trabalhar em conjunto para atingirem simultaneamente melhorias em custo (níveis de estoques e custos de produção) e nível de serviço (disponibilidade dos produtos). Para isso, foi necessário balancear demanda e disponibilidade de produtos (englobando produção e suprimentos) e volume e mix de produtos.
Resumo de Ganhos
O projeto da Nortegubisian, em conjunto com a equipe de melhoria de nosso cliente, gerou resultados significativos que estão destacados a seguir.
- Melhor organização, limpeza e mais segurança nos ambientes de trabalho
- Aculturamento para melhoria contínua
- Redução de 20% na média de capital em estoque
- Eliminação da falta de materiais de embalagem
- Otimização do espaço utilizado para guarda de matérias primas
- Compras de embalagens realizadas com base na demanda e consequente nivelamento da cobertura de estoque.
- Redução de 80% do tempo de cobertura (aumento de giro) para 20% das embalagens
- Nova política de compras baseado no novo modelo de gestão de demanda (Redução dos níveis médios de estocagem)
- Aumento do giro de estoque dos produtos acabados e eliminação de perda de produtos por shelf life
- Redução de 27% nos custos gerais de fabricação
- Redução de 75% de pedidos não atendidos com produtos em estoque
- Redução da falta de insumos em 90%
- Redução de 88% no lead time de planejamento a implantação do S&OP e ferramenta de previsão de demanda
- Aumento de disponibilidade da produção:
- 5,7% devido ao modelo de gestão de embalagens
- 6,0% devido à programação de abastecimento
- 4,6% devido ao modelo de sequenciamento
- Melhoria no processo de picking com redução no tempo de carregamento e expedição dos caminhões
- Processos documentados epessoal treinado para a garantia da sustentabilidade das ações
- Aumento de 28% de capacidade produtiva já observado no primeiro mês após a implantação dos planos de ação
Publicado em 08 de novembro de 2018.